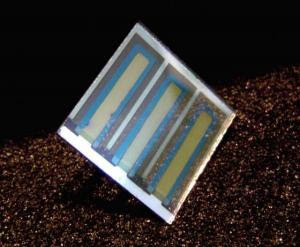
An organic photovoltaic cell on glass. The goal for UA scientists is to understand and control the interfaces in these devices at nanometer-length scales (less than 1/100,000 the thickness of a human hair) to enable the development of long-lived solar energy conversion devices on tough, flexible and extremely low-cost plastic substrates. (Credit: Image courtesy of University of Arizona)
----------------------------------------------------------------------------------------------------------------------------------------------
On a 104-degree Friday in July when sunlight bathed The University of Arizona campus, doctoral student Dio Placencia sat before a noisy vacuum chamber in the Chemical Sciences Building trying to advance the renewable energy revolution.
As a member of UA professor Neal R. Armstrong's research group, Placencia conducts research aimed at creating a thin, flexible organic solar cell that could power a tent or keep a car charged between trips to work and back home again.
He's passionate about renewable energy and says it's a waste that so little solar has been incorporated into society. "I have a little flat panel that I walk around with," Placencia said. "I usually put that on my backpack, and I charge my cell phone when I'm walking to school."
The sun is clean and free. "Here it is," he said. "Why not use it?"
Across the University, professors, researchers, students and others involved in policy planning and economic analysis are working to make that question moot. In a region noted for abundant sunlight, they are chipping away at problems like how to employ solar at the utility-generating plant level, how to harness it to charge the newly indispensable products of the day – cell phones, MP3 players, laptops – what to do at night and when clouds halt the energy giveaway from the sky.
The research proceeds in labs amid state-of-the-art equipment funded by multimillion-dollar federal grants. It's the product of students' hunches and long careers spent unlocking the mysteries of science. Along the way, students are being immersed in a nascent industry that many hope will be the economic engine of the next decade.
"Looking at renewable energy is a perfect place to emphasize that we don't know where the next breakthrough is going to be," said Leslie P. Tolbert, UA vice president for research, graduate studies and economic development. "Somewhere in a lab someplace, there's somebody figuring out a whole new way to capture sunlight. In fact, there are many people doing that. And even they are depending on knowing that there is, behind them, a cadre of basic science researchers producing new information that will feed their thoughts."
Armstrong, a professor of chemistry and optical sciences at the UA, occasionally teaches freshman chemistry. He decided one day near the end of the semester to try to make the material even more relevant. "I said to myself, well, lithium ion batteries in my cell phone, in my iPod," – his daughter had given him one – "I wonder how much coal we burn to charge those guys up at the end of the day. Because that's one of the big drivers for portable power, to get all this stuff off the grid." After making some very conservative calculations, he arrived at an answer, which he shared with the class: "You burn about a quarter of a pound of coal per charge of your lithium ion battery, and you generate about half a pound of CO2 per charge, per battery, per day .... The room got really quiet."
The next time, he intends to calculate how much coal is burned per Twitter tweet.
"It really is chilling," Armstrong said. "You start doing the math and thinking about the number of consumer electronic devices that you and I have added to our lives in the last decade that I charge up typically once every night – my laptop computer and my cell phone. Then you start thinking about, 'What if I do buy an electric car, and I come home at night and plug that sucker in,' and you do the same thing. We'll shut this grid down in no time."
In April, the U.S. Department of Energy announced it was funding Armstrong's Center for Interface Science as one of 46 Energy Frontier Research Centers. The mission of these centers, which will receive $2 million to $5 million a year for five years, is "to address current fundamental scientific roadblocks to clean energy and energy security," according to the DOE.
Ever since Armstrong was a graduate student during the first Arab oil embargo in 1973, he's experienced a succession of government distress calls over energy. One such emergency led him to discover the work of Heinz Gerischer and Frank Willig in Germany. They had figured out how to adsorb dye molecules to the surface of oxides and split water with light from the sun. "I thought, 'That's it. That's what I'm going to do my career on.'"
He moved to the UA in 1978, attracted by a program in photo-thermal solar energy conversion. In the 1980s, with gas cheap and plentiful again, solar went back on the back burner.
The next call came about four years ago. "DOE was beginning to sense that the tides were about to shift again, big-time," Armstrong said. "And they were really concerned that they didn't know what to do – how to present this to Congress in a way that would lead to new funding and which would have a rationale associated with it so that by the middle of this century we had someplace to go."
Armstrong realized it was time to come back to the problem that he wanted to work on 30 years before. "This time, we were really well-equipped," he said. "We've learned how to image molecules at the molecular level, we've learned how to measure energies of incredibly thin films, we've learned how to make devices, we've collaborated with physicists and material sciences and that sort of thing, we've done a lot of interesting other stuff and I suddenly realized I could bring it all back together here."
In his office, he displays a sample of his work: a 1-inch square of glass on which is deposited a thin film of indium tin oxide, a conducting transparent oxide commonly found in display technologies like computer screens. On top of that is a thin film of organic dyes. The last layer is an aluminum electrode.
"You'd have a roll of plastic with these cells laid out on it," he explained. "The idea is for you to go to Target or something like that and buy this roll of plastic and roll it out. It's got two wires connected to it, and you plug in your battery or your laptop and charge it up."
"The grand total in terms of the thickness is about 400 nanometers, which is one ten-thousandth the thickness of a human hair. And yet, shine a light on it and you get electricity out of it. Now we'd like it to be a bit thicker. We have to keep them thin in order to get all of the electrical charge out of the device. But if you think about this as a sandwich structure, we've made this incredibly thin sandwich and then each of the layers in contact with each other have to be just right in terms of the chemical composition, the orientation of the molecules, how well they adhere to each of the underlying surfaces. And if I go in and change just one molecule layer, the composition – that's at the level of 1 nanometer in thickness – I can take a good device and turn it into a bad device; I can take a bad device and turn it into a good device. That's the kind of level of control that we need. And we don't fully understand it."
But the equipment available now – optical microscopes capable of imaging individual molecules and revealing their electrical properties and spatial orientation – are helping his team understand. His goal is to figure out how to have the molecules arrange themselves – every time – in a way to produce lots of electricity. "They have to all line up like little soldiers," he said.
"We have to give you a technology that is going to look like an ink, like a blue ink, that you can spray down on one of these surfaces and the molecules at the nanometer level are going to say, 'OK, we're going to get organized this way,' and in doing so, when I put that top electrode on and shine a light, I'll get lots and lots of electricity out of there," Armstrong said.
A high vacuum photoelectron spectrometer allows them to build each molecular layer, moving it within the vacuum to study it, and then continue with another molecular layer. Other tools, like a silicon microtip, which looks like a tiny phonograph needle, can be positioned to +/- 0.01 nanometers. "Well inside the diameter of a molecule," he said. Bouncing a laser off the back of the tip yields an image. Passing current through the tip, they can map the electrical properties of molecules. All this can help them build a template to create the ideal array of the molecule assemblies.
Erin Ratcliff joined the team as a postdoctoral electrochemist with a doctorate from Iowa State. "My background wasn't in solar cells at all," she said. "I had to come here and had to learn everything, where grad students get it from Day One at the UA."
She spoke of the business school curve, resembling a hockey stick, when progress begins to accelerate rapidly. "We're right at the magic moment when the hockey stick starts to take off, when you go from flat to hockey stick. We're right there. It's exciting to read the literature and hope that, yes, we will take off. It will be exciting to look back and say 'I was there for that.'"
Email or share this story:
|
More
Story Source:
Adapted from materials provided by University of Arizona.
No comments:
Post a Comment